Determining accurate kWh savings:
Addressing inconsistent meter readings with Power Corporations’ General Managers – improvements are happening
Increased use of energy for some post retrofitted homes:
Pre and post surveys being conducted to determine reasons such as increased number of occupants, less wood being burned and more baseboard heating use
Shipping products and tools – cost effectively and timely:
Order construction products in the fall, for delivery on the winter road, for work to be done the following summer- to avoid costly shipping by air
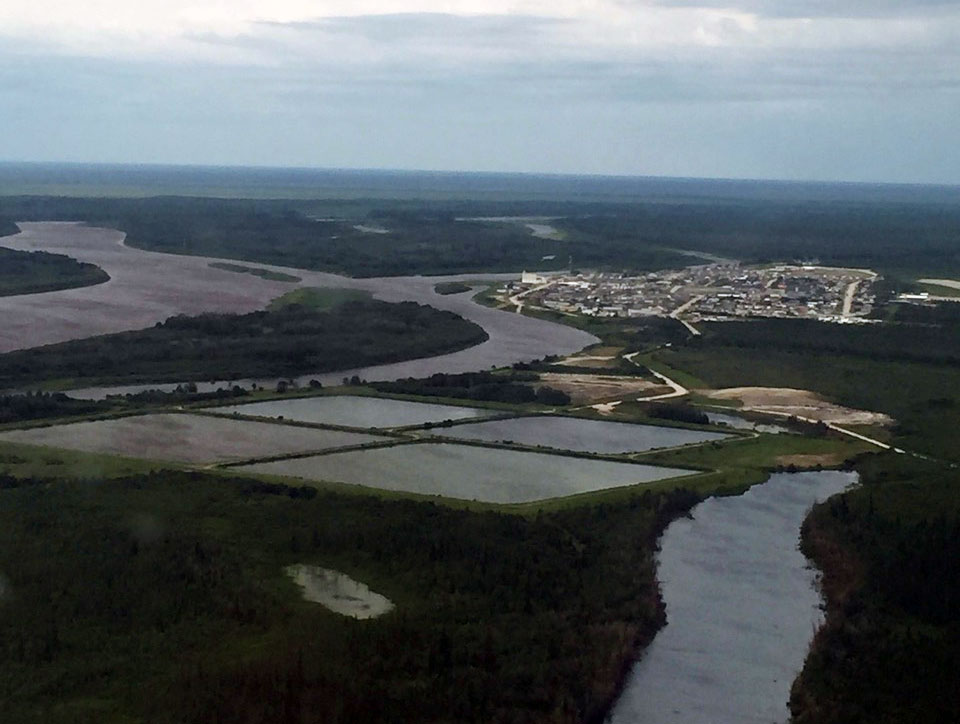
Retrofit Challenges: Remote communities such as Kashechewan have challenges obtaining supplies and materials.
Building local skills capacity to ensure qualified foremen and crew:
- 5 weeks training each spring – classroom and hands on
- Ongoing technical support, weekly calls
- Some crew members gained apprenticeship hours
- Ensure safe working environment – extensive safety training and safety equipment provided and enforced
Condition of the homes presents retrofit challenges:
Many homes have wet foundations, curled shingles, no siding, rotting wood, missing ceiling poly and tiles, holes in floors. Work collaboratively with Housing Managers to do necessary repairs prior to COTC energy retrofit work.
Challenges With HRV Units: Often Turned Off
Balanced mechanical ventilation is an essential element of a comprehensive energy retrofit, but often turned off to “save money”.
- COTC Foreman and CCs educate the occupants on health benefits of HRV and how to adjust controls for ultimate comfort
- COTC HRV maintenance labels and info brochure in development
- COTC in discussion with Housing Managers to provide more HRV maintenance help to occupants
- 1 KW heaters installed to boost air temperature are resulting in high energy bills – they are not necessary
Some people refuse to have an HRV installed.
They believe it is too costly to use and uncomfortable.
- Occupant must sign a waiver that they understand the consequences
- Need to continue educating occupants on the health benefits and how we are installing the supply in the ceiling versus in the wall or in the floor to reduce discomfort and the units will be installed properly with balanced flow
Lack of local skilled labour to install and maintain HRVs properly.
- OTC partnered with CMHC in 2016 for HRV training, included Housing Staff
- COTC and AFN partnered with Mushkegowuk Council in 2017 for funding to hire exclusive HRV installation crew in Attawapiskat
- (Considering the same for Fort Albany and Kashechewan)
Homes built on wet soil / muskeg in the James Bay Lowlands.
Working with Housing and Chief and Council to try different foundation options that are better suited to the muskeg
Time lost for set up and set down.
Bought utility trailers to carry equipment and tools to the site each day – reduces time moving equipment back and forth from stationary locked trailers
Time lost for cultural breaks and funerals.
Built in extra time for work per house to allow time to respect families
Lack of local qualified electricians and high cost to fly in electricians.
Mennonite Central Committee – provided volunteer electricians, COTC paid expenses
Challenges that we have little control over:
- Gas shortages
- Shorter warm weather working time
- Level of existing local skills for HRV installation, electrical and plumbing
- Evacuations of the communities for spring break up of the rivers